WELCOME
Weekly selected highlights in flow control, treatment and combustion from the many McIlvaine publications.
- Largest Coal Fired Power Pump Market is in the RCEP
- Fabric Filter Market for Coal Fired Electric Generators is Growing Faster than the Industry
- Frac Sand Plant CFT Decisions is now Available
- IAC is the First Major Sponsor of Frac Sand Plant CFT Decisions
- Let’s meet in Houston on the 26th
Largest Coal Fired Power Pump Market is in the RCEP
Most of the new coal fired power plants will be built in Asia. The region already operates more coal fired power plants than the rest of the world. The U.S. has willingly given up its quest through the Trans Pacific Partnership to be a major player in the Asian coal fired power combust, flow, and treat (CFT) market. International CFT suppliers are unwillingly losing an advantage which will be difficult to overcome. A new trading group in Asia includes Chinese financing for plants throughout the region. The plant suppliers include a number of large Chinese companies.
The Trans-Pacific Partnership (TPP), which has now been rechristened the Comprehensive and Progressive Agreement for the Trans-Pacific Partnership (CPTPP) includes the Regional Comprehensive Economic Partnership (RCEP) – a free trade deal involving the ten members of ASEAN plus its six dialogue partners. If it succeeds, RCEP will become the world’s largest trading bloc, accounting for 3.4 billion people with a total Gross Domestic Product (GDP) of $49.5 trillion.
China has more than 40 percent of the existing coal fired boiler fleet. It has 80 percent of all the coal fired power plants less than 20 years old. This means that much of the experience with newer pump designs resides in China.
Coal fired power will remain the largest purchasing segment in the world power industry over the next five years.
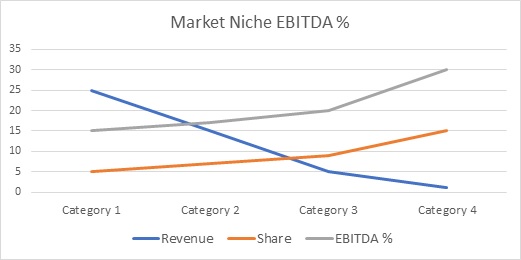
Most of the pump purchases in RCEP power plants will be for coal fired generation. The new coal fired capacity will exceed the new gas turbine capacity. Coal fired power plants spend 3.5 times as much for pumps as do gas fired plants. Solar and wind pump purchases are small.
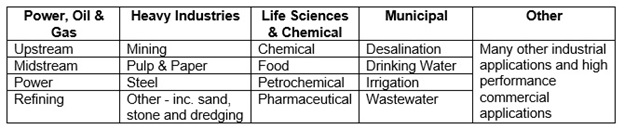
Outside of the RCEP the two most active constructors of coal fired power plants are Turkey and Pakistan. Due to the China-Pakistan Economic Corridor plan and billions of dollars of Chinese funding for seventeen coal fired power plants, Pakistan is nominally part of this larger endeavor. China and Turkey have strengthened relationships and China is investing in Turkish power plants. So China is involved in all the regions with coal fired boiler construction activity.
RCEP will be the major purchaser of power plant pumps over the next five years.
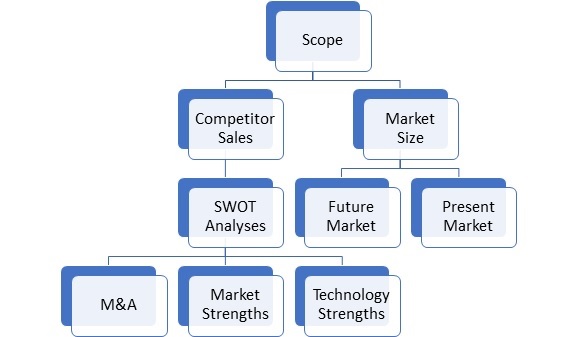
Environmental upgrades have been a good source of pump business. For example a limestone scrubbing system for a coal fired plant requires an investment of more than $100 million. Of this total over $2 million is for pumps. The addition of 200,000 MW of FGD systems in the U.S. spread out over three decades resulted in less than $1 billion of dollars of revenue for pump companies. China has now installed over 900,000 MW of FGD systems. Other countries in RCEP will need another 400,000 MW of new and retrofit systems. India is presently retrofitting more than 50,000 MW of FGD.
Repair parts and maintenance for pumps used for recycling limestone slurry is substantial and represents a larger expenditure over the pump life than does the original investment. So the combined market for new pumps and repairs in the power industry will exceed $3 billion in 2019.
Detailed power plant pump forecasts are provided in N019 Pumps World Market
For more information contact Bob McIlvaine at 847 784 0012 ext. 122 rmcilvaine@mcilvainecompany.com
Fabric Filter Market for Coal Fired Electric Generators is Growing Faster than the Industry
Coal fired power plants around the world will increase expenditures for fabric filter systems, bags and third party maintenance services by more than seven percent per year. The total market will be $3 billion by 2020.
Fabric Filter Market 2020 - $ millions
|
|
Dry Scrubber
|
Particulate Only
|
Total
|
Hardware and Construction
|
400
|
600
|
1000
|
Bags, Cages, other Repair Parts
|
250
|
400
|
650
|
IIoT and Remote O&M Potential
|
500
|
800
|
1300
|
Total – Advise, Design, Supply, Construct, Guide, Maintain
|
1150
|
1800
|
2950
|
There are a number of positive and negative impacts on future fabric filter related sales to coal fired generators around the world.
· The coal fired boiler capacity in Europe and the U.S. will shrink but will be more than offset by new Asian capacity.
· New plants will continue to select precipitators for more new capacity than will choose fabric filters. However the share for fabric filters will slowly increase.
· Some existing plants with precipitators which are not meeting emission limits are installing bags within the existing precipitator shell.
· Dry scrubbing and Dry Sorbent Injection (DSI) are gaining market share although wet limestone FGD is still the dominant choice.
· Catalytic ceramic filters are not expected to gain much penetration by 2020 but will potentially be the first choice for power plants in later years.
· New technical developments are shaping the forecast and create substantial unknowns.
Fabric filters can produce consistently low particulate emission rates. They are not impacted by changes in the coal. Electrostatic precipitator performance is affected by coal variations. Where mercury regulations are stringent activated carbon injected ahead of the fabric filter can result in higher removal rates than injection ahead of a precipitator.
Dry scrubbing involves less capital expense than limestone wet scrubbing. Direct sorbent injection has very low capital expense other than the fabric filter. However, reagent costs are high. Where stringent regulations are forcing scrubber additions but boiler life is limited, dry methods are more cost effective.
The fabric filter filter cake provides final absorption in dry scrubbing and DSI systems. Presently the cleaning of filter bags is done to optimize particulate removal. There is significant potential to optimize acid gas removal as well as particulate with new cleaning technology. Ceramic filters with embedded catalyst in conjunction with DSI are the lowest cost approach to remove particulate, NOx and acid gas. This is because only one vessel instead of three are needed. The approach has worked well with 3 meter bags on applications with relatively low air volumes. Longer bags are now being commercialized. This could lead to widespread use by coal fired electric generators.
A forecast of this market potential is provided in N021 World Fabric Filter and Element Market
All the existing and proposed fabric filter installations on coal fired boilers are tracked in 42EI Utility Tracking System
For more information contact Bob McIlvaine at 847 784 0012 ext. 122 rmcilvaine@mcilvainecompany.com
Frac Sand Plant CFT Decisions is now Available
A free website now provides continuing insights relative to frac sand plant combust, flow and treat (CFT) decisions. When you register you not only have access to the site but you will also receive this Monthly Alert. You will also be notified of free webinars in which you can participate
In an industry which is evolving as rapidly as frac sands it is difficult to select CFT products and services which will achieve the lowest total cost of ownership results. The lowest initial priced product may not prove to the best choice over the long term. But in an industry which is evolving the life cycle costs have to be anticipated rather than resurrected. Wisdom has to be substituted for facts.
The performance of a product in the asphalt, gravel, foundry or mining industry may or may not be relevant in this new application. On the other hand the resin coating of sand for foundry cores and molds is a technology which is greatly advanced thanks to many decades of evolution to meet the challenges of very high temperatures and moderate pressures. Wet sand plants challenge the slurry pump manufacturer due to the abrasive nature of the product. On the other hand slurry pumps materials technology including hard coatings has mastered the toughest mining challenges.
The Industrial Internet of Wisdom is a concept which can leveraged by the frac sand industry to
· Learn from the experience in other industries
· Take advantage of the experience being gained each day in frac sands
· Identify the new processes and products which can move the industry forward
Due to the remote location of frac sand plants and transload facilities the benefits of remote monitoring and control are even greater than if the operations were concentrated conveniently. The mining industry is moving forward with IIoT and Remote O&M. Rio Tinto is planning on completely automating all of its operations and eliminating personnel in the mines. Driverless trucks and trains are already commonplace. The frac sand industry will be able to take advantage of the mining IIoT experience.
IAC is the First Major Sponsor of Frac Sand Plant CFT Decisions
It is fitting that Industrial Accessories Company (IAC) is the first major sponsor of this service The company is a leader in the frac sand industry. The extent of its activities is apparent when you click on IAC under corporations in the intelligence system.
Future Proof Your Plant to Meet Tomorrow's Emission Standards
New IAC designed sand plant runs at 268 tph with emissions of just 0.0017gr/dscf
IAC supplying pneumatic conveying systems in many industries
IAC provides operational expertise, programming and maintenance support to Preferred Sands
IAC is a turnkey system supplier for cement, ethanol, biomass and steel plants
IAC works closely with Nucor as a customer and supplier
Frac Sand Plants Need to Meet OSHA’s New Silica Exposure Rules
IAC Frac Sand Plant Optimization
IAC Completes 2 Frac Sand Plants in Poteet and Monahans Texas
IAC Dual Feed Rotary Dryer Provides the Precise Frac Sand Parameters Need and Saves Energy
The company recognizes the advantage of offering a range of services to owners which span the life of the plant. These can be summarized as Advise-Design-Supply-Construct-Guide-Maintain.
Advise: IAC prioritizes the ability to understand the customers goals and to advise from project inception. IAC has pursued this approach by hiring as its new president, a senior executive from one of the sand and aggregate operating companies. In one recent presentation IAC Frac Sand Plant Optimization Bob Carter described a multi-step process to achieve an understanding of the various control points and the impact or change each introduces to a sustained operation. The six steps are: 1) characterization of each type of optimization. This would include water related processes such as filtering, settling and spill management. 2) Operate the plant and gather data compared to original design para. 3) Model impact of operational parameters like feed gradation on control points. 4) Develop Operational SOP's around control point optimization. 5) Measure and report results and progress at all levels of the organization. 6) Approve capital expenditures around advanced control, retrofit, design modifications, etc., targeted toward specific control point optimization.
Design: With its extensive process knowledge IAC is designing large systems for a number of manufactured sand plants as well as for clients in aggregate, cement, and steel. Understanding of components and their impact on total cost of ownership is critically needed by the designer. If there is a better fan or pump for the application it should be selected by the designer. Since these components last for a decade or more the initial design is a major factor in long term operation and maintenance.
Supply: The company has its own designs of dust collectors, pneumatic conveyors and a newly patented dual fired rotary dryer/cooler. Developments such as high temperature catalytic filter elements are routinely assessed. IAC has decades of experience in selecting and supplying all the components. The company has a number of electrical engineers creating motor control centers and is poised to take advantage of all the new IIoT opportunities.
Construct: IAC has a subsidiary construction company, Adelphi, which has a long proven record of delivering on time and at competitive prices. For this reason IAC has been the firm of choice for a number of owners of frac sand plants who needed accelerated construction to take advantage of the in basin trend.
Guide: The company has strong expertise and guidance programs for many components but also in meeting environmental emissions requirements. It helps with permit applications and can send a team to the site to measure fugitive emissions and help institute hardware and operational changes to achieve the desired results.
Maintain: The need for quick delivery of critical parts is addressed with an efficient system decades in the making which supplies 20,000 different parts and components such as valves, hose, cages, bags, and blowers. Service includes complete programs for monitoring and replacement as needed. Other options include training and operations. A program is in place to organize and rely on the continuing flow of evidence regarding component performance. As IIoT and data analytics provide even greater quantities of evidence the company is organized to utilize it.
Let’s meet in Houston on the 26th
The North American Frac Sand Conference 2019 will be held in Houston on February 26 and 27. The objective is to bring the frac sand supply chain industry together to evaluate solutions for overcoming the current market and logistical challenges of supplying frac sand to well sites. Registration details are found at https://www.frac-sand-conference.com/
In our previous Alert we listed the exhibitors. Screening is a crucial step in creating the best proppant. If you extract names from the exhibitor list and then search for them under “corporations’ in the Decisions you find
Astec claims first single source dry plant for proppant
FRAC PACK (STATIONARY, RELOCATABLE OR PORTABLE) according to Astec is the industry’s first, full, single-source dry plant for the proppant (frac sand) and other sand processing industries. Astec says it is engineered from the ground up to withstand non-stop operation, 24 hours per day, 7 days per week, 365 days per year, year after year. As the United States’ largest manufacturer of asphalt plant equipment, Astec cites its reputation as the most resilient drying, storage systems, and controls, with world renowned service. A sister company, Kolberg-Pioneer, manufactures what the company claims to be the toughest, most versatile, and most efficient screens available. The company is a sponsor of North American Frac Sands 2019, so these claims can be pursued first hand. We will be adding additional articles such as this one to the Frac Sand Plant Decisions. These articles will provide the background evidence to validate various claims.
Revision Date: 1/17/2019
Derrick wet and dry screening technology used in frac sand plants
Derrick’s patented Stack Sizer® high capacity, wet sizing technology – as well as the latest in Derrick dry screening products will be displayed at the Derrick stand at North American Frac Sands 2019. Paul Brodzik, Glenn Geles and Travis Rice also discussed Dewatering Machines, and Polyweb® Urethane Screens used to improve frac sand production by wet sizing only at the 7th Annual Frac Sand Supply & Logistics Conference last October.
Revision Date: 1/11/2019
Tags: 211111 - Crude Petroleum and Natural Gas Extraction ????????, 211111 - Crude Petroleum and Natural Gas Extraction ????????, 212321 - Construction Sand and Gravel Mining , Derrick Corp, Screen
SWECO screens tailored for frac and resin coated sands
The SWECO Gyratory Sifter line of equipment was specifically designed with the proppant industry in mind. Utilizing a uniform gyratory motion, the SWECO GyraMax™ and BigMax™ Gyratory Sifters provide superior performance when high capacity, efficiency, and accurate screening is required. FRAC SAND --Grading Screens: the combination of uniform circular motion and retention time provides high capacity classification of multiple grades to API Specs ... even with high percentage of nearsize in the feed Polishing Screens: GyraMax and BigMax screens can be added to existing plants to clean up off-spec product produced by less accurate legacy screening equipment. RESIN COATED SANDS: Circular motion effectively removes agglomerates and screens out fines for product uniformity and consistency-- Inlet turret with perforated plate rejects “clinkers” and protects screen mesh --Special high temperature features ensure reliable operation even with 350o F fee
Revision Date: 1/10/2019
Tags: 211111 - Crude Petroleum and Natural Gas Extraction ????????, 211111 - Crude Petroleum and Natural Gas Extraction ????????, 212321 - Construction Sand and Gravel Mining , Sweco, Sand, Screen
Terex revenues in material processing exceed $ 1 billion
Revenues in 2017 were $4.36 billion. Materials processing accounted for 25% of the total. Net income was $126 million. There are 10,000 employees with 50% in the U.S.---Materials processing equipment is used in processing aggregate materials for building applications and is also used in the quarrying, mining, demolition, recycling, landscaping and biomass production industries. Materials processing equipment includes crushers, screens and feeders, washing systems as well as wood and biomass chippers.---- Heavy duty inclined and horizontal screens and feeders are used in low to high tonnage applications and are available as either stationary or heavy-duty mobile equipment. Screens are used in all phases of plant design from handling quarried material to fine screening. Dry screening is used to process materials such as sand, gravel, quarry rock, coal, ore, construction and demolition waste, soil, compost and wood chips. --- Feeders are used to unload materials from hoppers and bulk material storage at controlled rates. They are available for applications ranging from primary feed hoppers to fine material bin unloading. The range includes apron feeders, grizzly feeders and pan feeders. Washing system products include mobile and static wash plants incorporating separation, washing, scrubbing, dewatering and stockpiling. Terex manufactured mobile and stationary rinsing screens, scrubbing systems, sand screw dewaterers, bucket-wheel dewaterers, hydrocyclone plants for efficient silt extraction and a range of stockpiling conveyors. Washing systems operate in the aggregates, recycling, mining and industrial sands segments.
Revision Date: 1/15/2019
Tags: 211111 - Crude Petroleum and Natural Gas Extraction ????????, 211111 - Crude Petroleum and Natural Gas Extraction ????????, 212321 - Construction Sand and Gravel Mining , Terex, Screen, Hydrocyclone, Separation, Crushing, Screening
Terex has different competitors in crushing screening and washing
Terex competes with other manufacturers based on many factors, particularly price, performance and product reliability. Terex generally operates under a best value strategy, where it attempt to offer customers products that are designed to improve customers’ return on invested capital. However, in some instances, customers may prefer the pricing, performance or reliability aspects of a competitor’s product despite Terex product pricing or performance. Terex does not have a single competitor across all business segments. Terex Competitors in materials Processing include ---- Crushing Equipment: Metso, Astec Industries, Sandvik, McCloskey, Komatsu and Kleemann--- Screening Equipment: Metso, Astec Industries, McCloskey, Kleemann and Sandvik----Washing systems McLanahan, Astec Industries and CDE Global.
Revision Date: 1/15/2019
Tags: 211111 - Crude Petroleum and Natural Gas Extraction ????????, 211111 - Crude Petroleum and Natural Gas Extraction ????????, 212321 - Construction Sand and Gravel Mining , Terex, Separation, Crushing, Screening
|