WELCOME
Weekly selected highlights in flow control, treatment and combustion from the many McIlvaine publications.
|
- Industrial Ventilation and Dust Collection should not be Two Different Silos
- Preparing for the Cement Conference in St. Louis
Industrial Ventilation and Dust Collection should not be Two Different Silos
Carefully engineered ductwork systems for frac sand plants (outdoors) have the same needs for optimum hood designs and balanced flow ductwork (without dampers) as industrial ventilation systems in foundries (indoors). Both have the same stringent regulations regarding silica dust. Industrial ventilation covers many types of air flow other than those ducted to a dust collector. On the other hand the ventilation design used at the pickup points in a dust collector system has a direct effect on the system cost and energy consumption.
A well designed hood utilizes only as much capture air as is needed. The cost of the dust collector is a function of flow. So a hood that requires twice as much capture air results in twice the system cost. A balanced ductwork system maintains the best velocity. It is not so high as to cause abrasion and excess energy consumption. It has to be high enough to insure that material does not deposit in the ductwork. Dampers need to be avoided because they cause turbulence and plugging. A correctly designed system uses tapered ducting and a constant duct velocity throughout the system. Also turbulence is avoided with gradual rather than abrupt changes in direction.
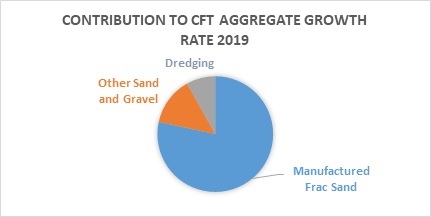
Minimum Turbulence Components Courtesy of ICAC-Intl
The concern for worker exposure to particulates is primarily focused on individuals working in environments such as foundries and coal mines where silica dust is generated. However, the concern for workers is just as great in frac sand plants and facilities which create toxic metal dust. John Brown of IAC-Intl in a recorded presentation linked from the McIlvaine Global Decisions Orchard reviews the needs and solutions for frac sand plants. He also references both primary and secondary lead plants where fine particulate emission limits are much lower than they are for silica.
There are a number of companies who are eliminating the two silos. CECO has acquired Kirk & Blum, a major ventilation contractor. It also acquired Flex-Kleen and other companies making air pollution control equipment. Nederman purchased MikroPul to complement its ventilation activities. In April 2018 it purchased Auburn FilterSense which makes triboelectric dust monitors commonly descibed as broken bag detectors. This gives Nederman a tool by which to remotely monitor the system operation and schedule bag replacement as needed for environmental and other reasons.
3M has introduced a blue tooth enabled pressure sensor which is inexpensive enough than it can be placed on every furnace filter. This technology has even more justification for use in industrial ventilation systems. Those systems dealing with toxic dusts have even more justification to install continuous monitoring devices.
Companies such as IAC-Intl, Nederman and CECO have the opportunity to be involved with industrial ventilation and dust control from the design and construction through the entire life of the system. New analyzers, data analytics and process management software make remote monitoring and O&M support very valuable. The biggest profit potential is total solutions. The supplier can provide a fixed price for O&M and replacement parts. With skilled remote operators, the cost to the owner can be less than if the O&M is handled in-house.
More information on this concept is contained in two McIlvaine publications
N031 Industrial IOT and Remote O&M
N021 World Fabric Filter and Element Market
Bob McIlvaine can answer your questions at 847 784 0012 ext. 122 rmcilvaine@mcilvainecompany.com
Preparing for the Cement Conference in St. Louis
The 61st Annual IEEE-IAS/PCA Cement Industry Technical Conference will be held in the St, Louis Convention Center, April 28-May 2, 2019. This is the largest conference in the cement industry and will include presentations of the latest technology covering a variety of topics important to the industry. There will also be Tutorials, Professional Training sessions, a state of the industry report and much more. There will be 150 exhibitors
McIlvaine has interviewed exhibitors in the past and posted this coverage plus other cement industry analyses and articles in a free site. These articles and interviews can be viewed at
http://www.mcilvainecompany.com/Decision_Tree/subscriber/Tree/UnivDB/appl3.asp?ref1=806&ref2=0&ref3=0&ref4=0&ref5=0&ref6=0
McIlvaine will be providing extensive pre conference coverage similar to that of WEFTEC in 2018 as shown at Municipal Wastewater Services and North American Frac Sands 2019 http://www.mcilvainecompany.com/Decision_Tree/McIlvaine%20Insights%20Issue%2089%20Jan%2011%202019%20Frac%20Sand%20Plant%20Alert.htm
There are lots of Combust, Flow, and Treat (CFT) products and services utilized in cement plants. Industrial Accessories Company. ( IAC-Intl), who will be one the conference exhibitors supplied a turnkey system for the Drake Cement plant in Arizona
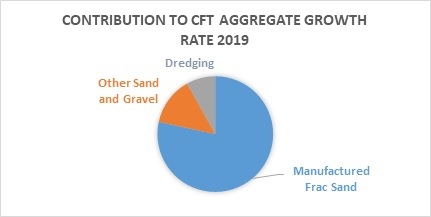
- Imported ingredients: Alumina and iron are imported as minor processing additions.
- Mining and crushing: Limestone (calcium) and silica are mined from the quarry and conveyed to the plant.
- Raw material storage: Limestone (calcium), iron, silica and alumina are stored in large silos.
- Blending: All raw ingredients are blended in proportion to prepare for grinding.
- Raw grinding: Raw ingredients are ground to fineness of baby powder and further blended into a homogeneous mixture.
- Heating and cooling: The ground mixture is fed into the kiln through a tall preheating tower, where it is heated and rapidly cooled to create clinker.
- Clinker storage: Clinker is stored in a large dome and silo waiting to be ground into cement.
- Finish grinding: Clinker is ground into the fine gray powder recognized as cement, adding a small amount of gypsum to control the time of setting.
- Cement storage and shipping: Finished cement is stored in a silo awaiting loading into trucks or rail cars.
IAC-Intl provided Design/Build services. The plant site sits on 300 acres in Drake, AZ. The facility includes complete raw materials receiving and storage, clinker production, rail loading and storage silos, coal fuel processing, and fugitive dust collection. The Design/Build contract was valued at $49.7 million. As part of the project, IAC supplied over 1,500 metric tons of structural steel, 34 different specially designed IAC OEM baghouses, energy saving IAC OEM air-to-air heater exchanger, conveyors, rotary valves, fans, and process control dampers for emission control at the plant.
The McIlvaine company tracks all the cement plant activity in N032 Industrial Plants and Projects
For more information contact Bob McIlvaine at rmcilvaine@mcilvainecompany.com 847 784 0012 ext. 122
|